Torque Checking System
Automate the manual laborious repeated task of checking the nuts for torque values and deciding the serviceability.
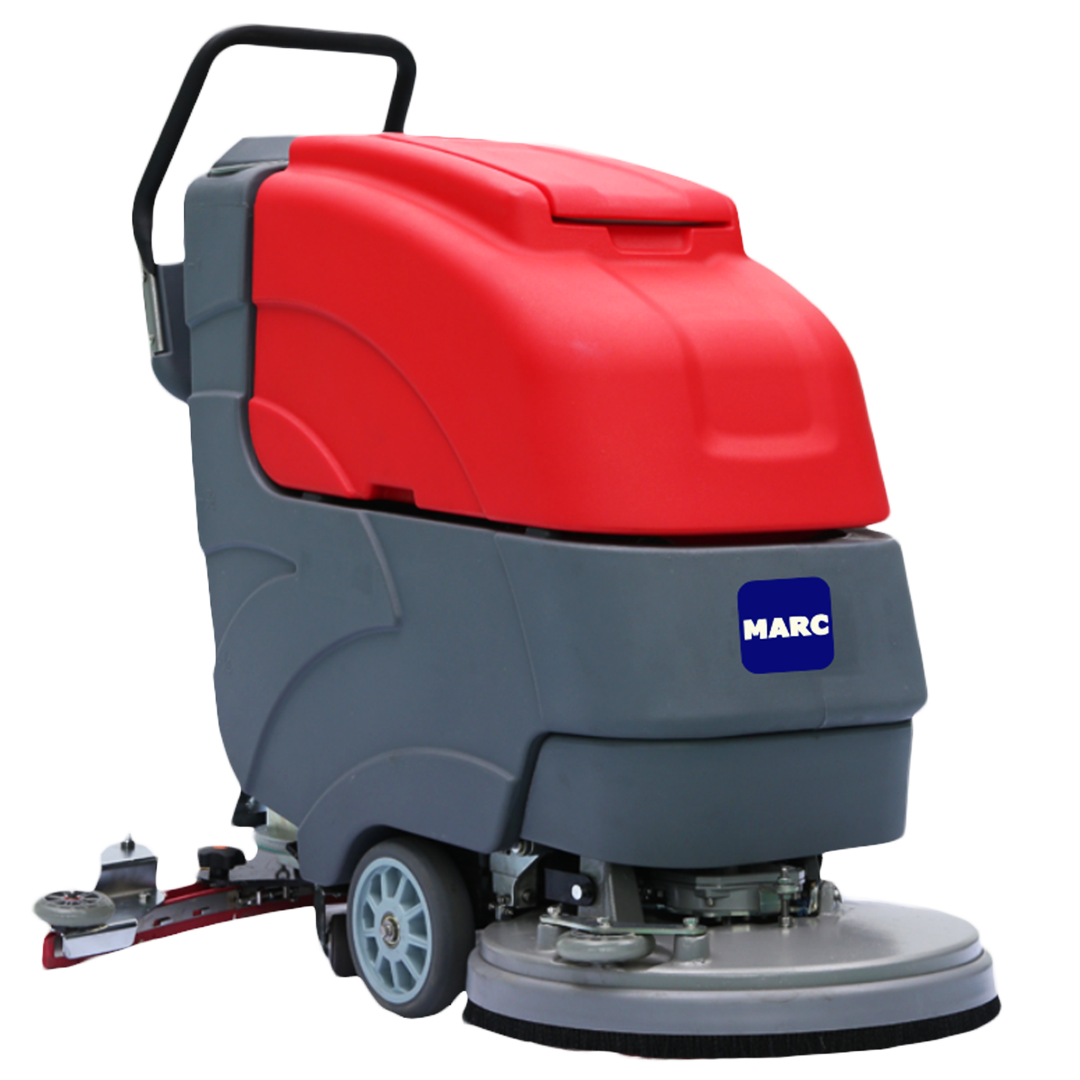
Technical Details
The torque checking system is a product designed and to measure and verify the torque applied to fasteners (nuts) in various applications. Ensuring proper torque is crucial in many industries, including automotive, aerospace, construction, and manufacturing, as it affects the safety, reliability, and performance of assembled components
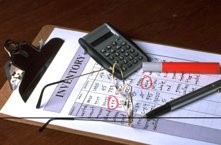
Technical Specifications
Base Technology
Torque sensors, also known as torque transducers measure the amount of torque applied to an object. Strain gauge principle of strain deformation in a material under stress. Strain gauges are attached to a torsion bar or shaft that deforms slightly when torque is applied. The strain gauges measure this deformation, and the data is then converted into torque values.
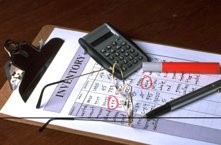
Cobot, incorporates a range of features that allow it to be used safely, directly alongside human workers and without the need to design and build bulky barriers or fencing. Cobot can continuously share workspace with people, giving it maximum flexibility and efficiency. Robot and human cooperate on the same tasks, without jeopardizing productivity or safety.
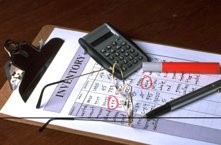
Supported Sizes
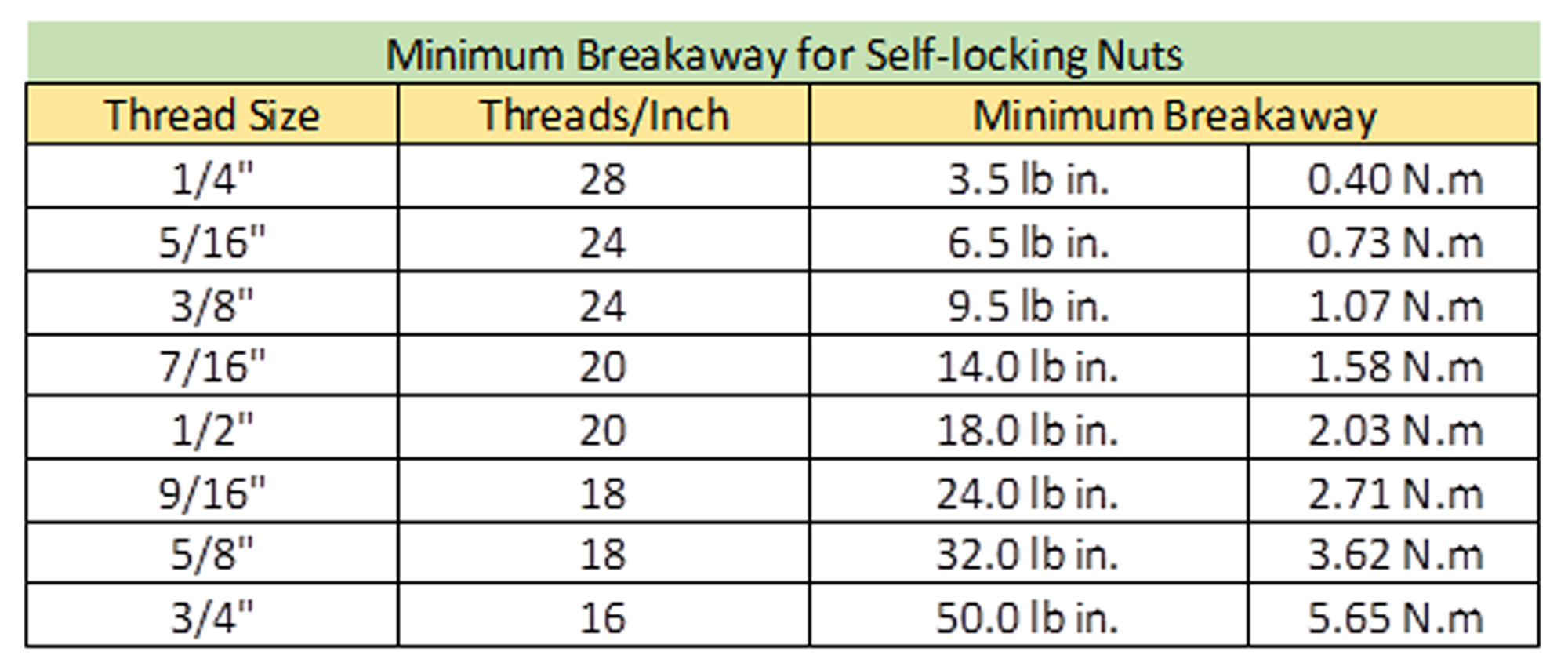
Key Hardware Modules
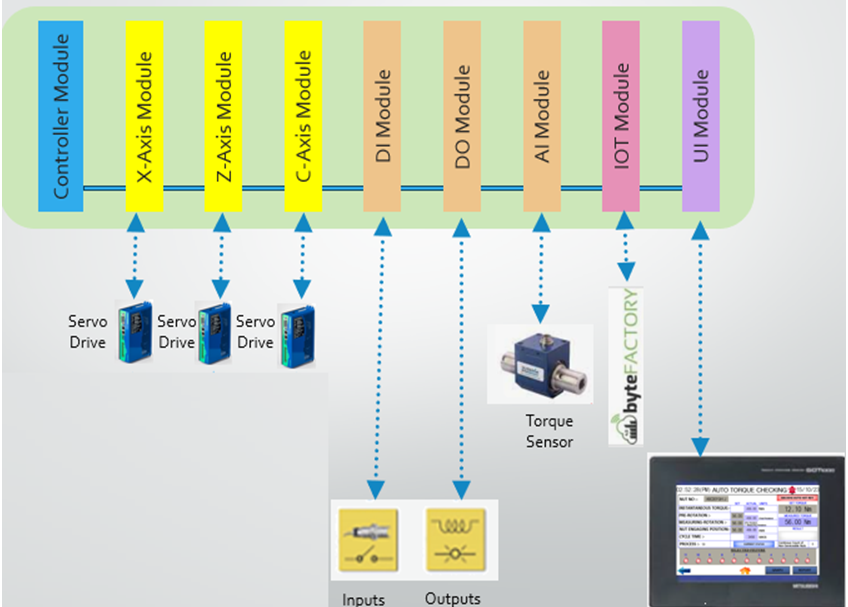
User Interface (UI) Features
The UI features a user-friendly touchscreen interface, allowing operators to interact with the HMI by touching and dragging elements on the display.
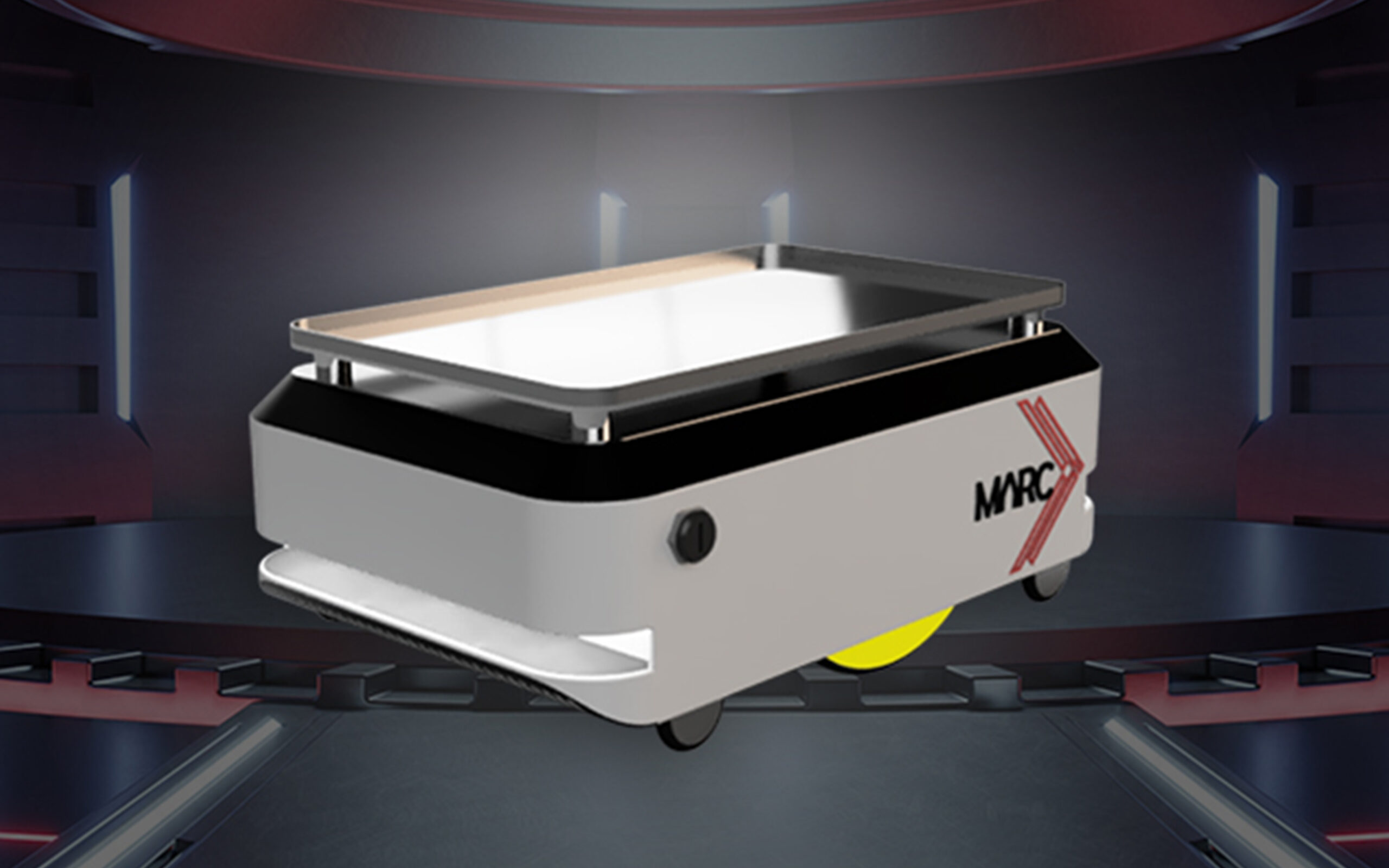
The UI comes with high-resolution color displays that provide clear and detailed visualization of process information and system status.
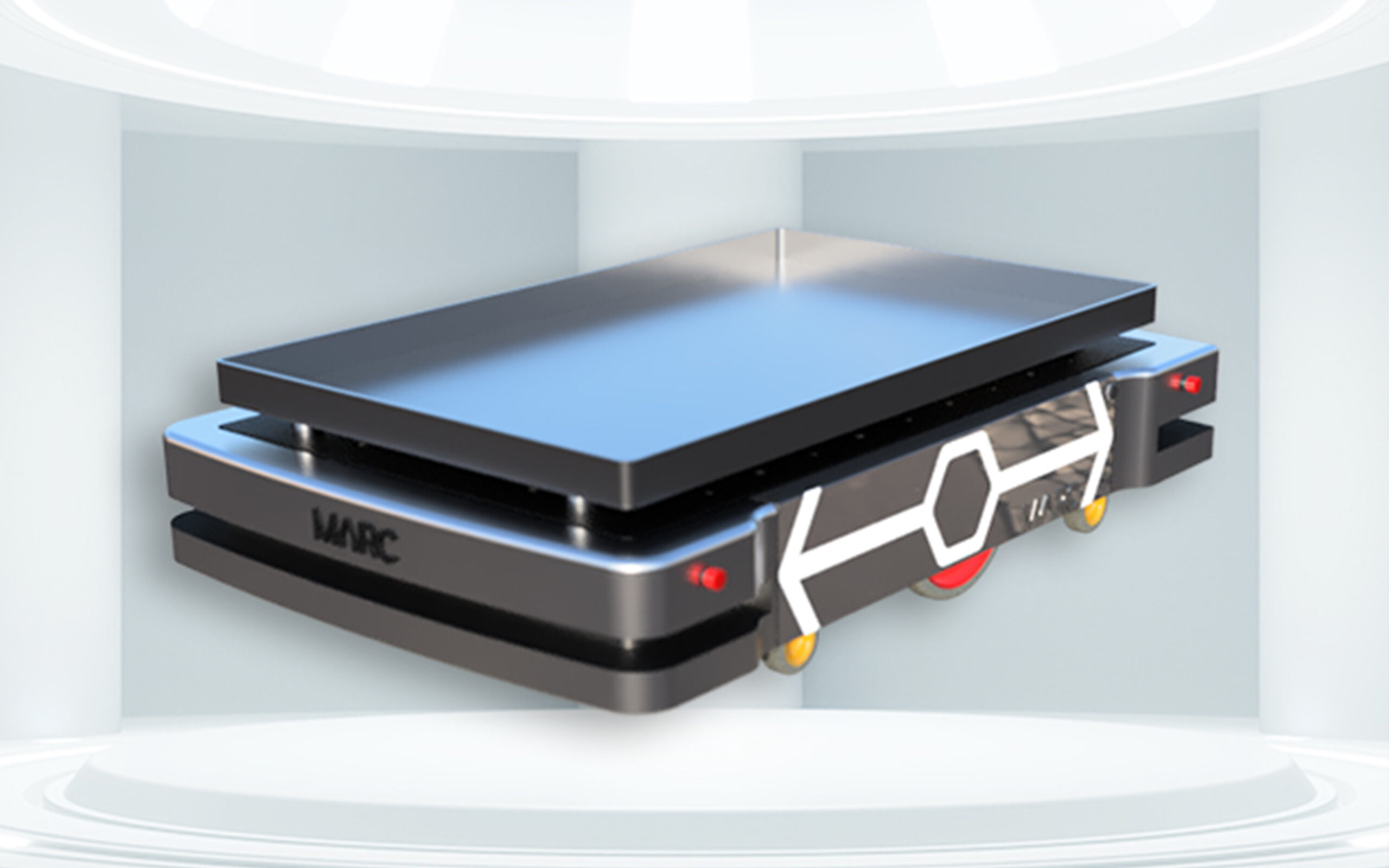
Support for various communication protocols, such as Ethernet, RS-232, RS-485, and others, to enable connectivity with a wide range of devices and networks.
UI offer multilingual support, allowing users to customize the interface language based on their preferences or operational requirements.
Some models provide data logging capabilities, allowing the HMI to store historical data for analysis and troubleshooting purposes.
Security features like user authentication and password protection to control access to certain functions and ensure the integrity of the system.
The UI’s can handle alarms and events, providing visual and audible alerts to operators when abnormal conditions occur in the industrial process.
Integrate with Internet of Things (IoT) devices for additional contextual information and enhanced connectivity within indoor spaces.
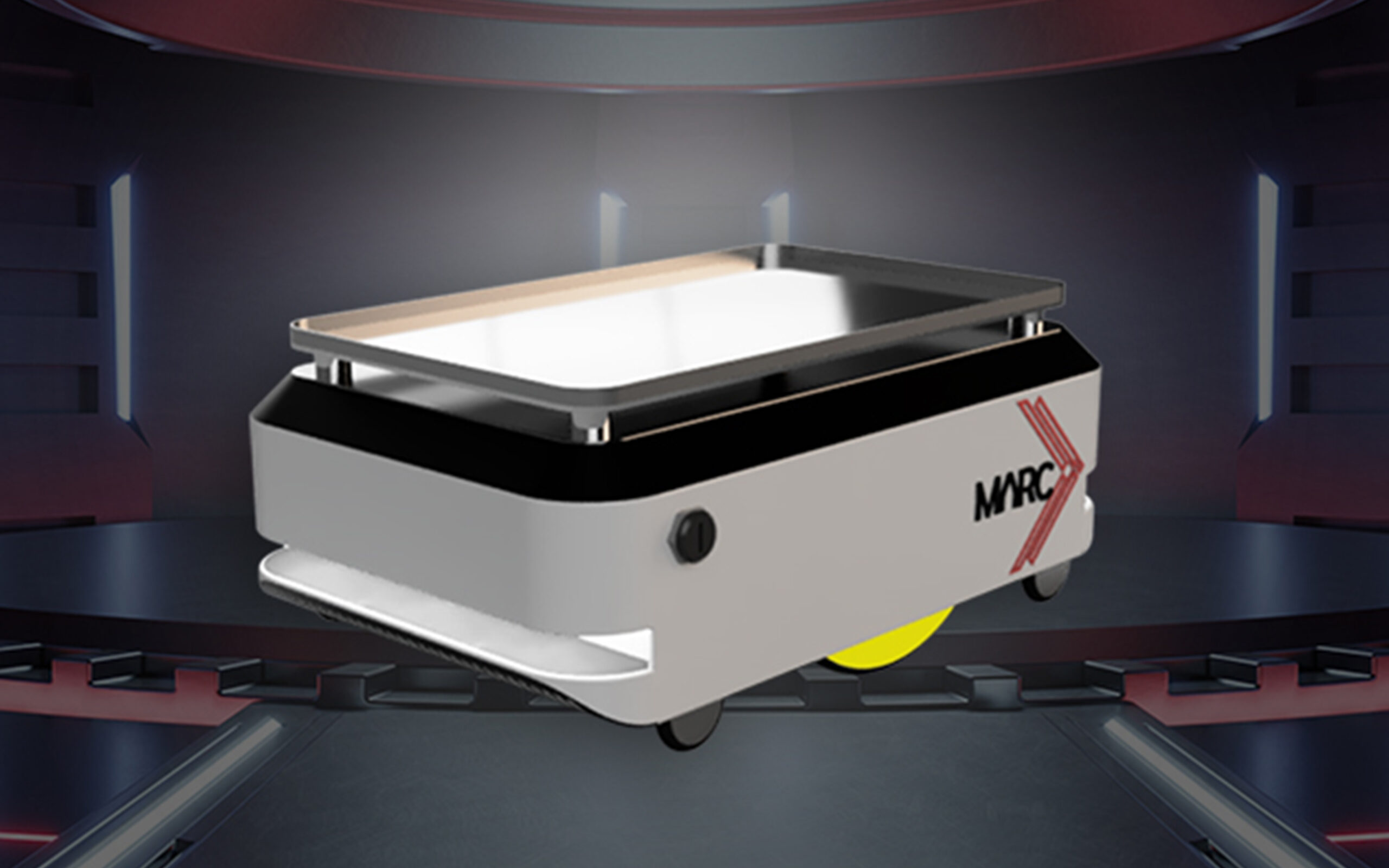
Benefits and Value
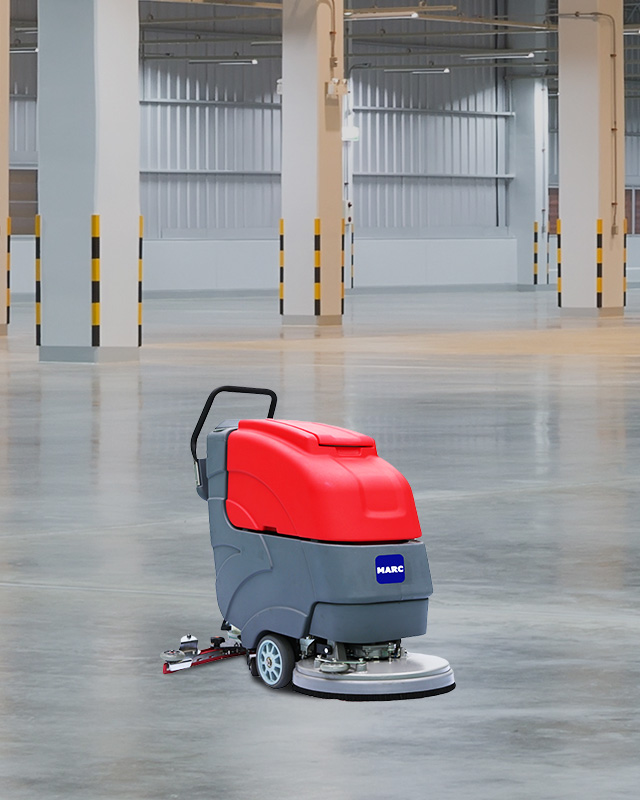
Use Cases and Applications
Automotive Manufacturing
In the automotive industry, torque checking systems are extensively used on assembly lines for the construction of vehicles. These systems ensure that bolts and nuts in critical components, such as engines, transmissions, chassis, and suspension systems, are tightened to precise torque specifications.
Aerospace and Aviation
Precision and reliability are paramount in the aerospace industry. Torque checking systems are employed during the assembly of aircraft components, engines, and critical structural elements. This ensures that fasteners are tightened to the correct specifications, meeting stringent safety and performance standards.
Heavy Equipment Manufacturing
Manufacturers of heavy machinery, such as construction equipment, agricultural machinery, and industrial machinery, use torque checking systems to ensure that bolts and fasteners are properly tightened. This is crucial for the safe and efficient operation of these heavy-duty machines.
Energy and Power Generation
Torque checking systems are used in the assembly of components in power plants, including turbines, generators, and other critical machinery. Proper torque ensures the structural integrity and performance of these components.
Rail Transportation
In the manufacturing and maintenance of trains and rail systems, torque checking systems are employed to ensure that fasteners in critical components, such as wheel assemblies, brakes, and structural elements, are tightened to the specified torque values.
Oil and Gas Industry
In the oil and gas sector, torque checking systems are used during the assembly and maintenance of equipment, pipelines, and offshore platforms. Proper torque is essential to prevent leaks, ensure structural integrity, and maintain the reliability of equipment in harsh environments.
Medical Device Manufacturing
Torque checking is important in the assembly of electronic devices and consumer goods. This includes applications such as the assembly of computer components, appliances, and other products where correctly torqued fasteners are crucial for functionality and safety.
Electronics & Consumer Goods
In the oil and gas sector, torque checking systems are used during the assembly and maintenance of equipment, pipelines, and offshore platforms. Proper torque is essential to prevent leaks, ensure structural integrity, and maintain the reliability of equipment in harsh environments.
Renewable Energy
In the manufacturing of wind turbines and solar panels, torque checking systems are used to ensure that fasteners are tightened properly. This is essential for the structural integrity and efficient operation of renewable energy systems.
Unique Selling Points (USPs)
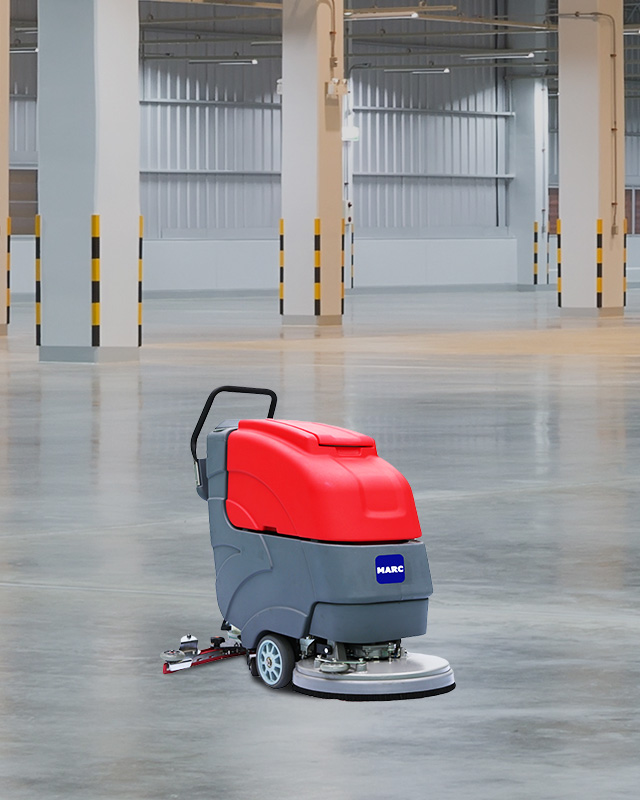
How It Works?
CLEANING MADE EASY AND AUTONOMOUS
Ready to Experience the Future of Commercial Cleaning?
Get the free demo on MARC Ax Cleaning Robot by filling out this form:
And talk to our Experts to know about:
- What are the Use cases?
- How does it work?
- What are the Benefits?
Our Recent Blogs
Industrial and Commercial Floors Cleaning Made Easy and Autonomous
Maintaining a safe and efficient working environment requires industrial cleaning. As a labour-intensive process, it…